Custom Robotic Palletizing Systems
As a FANUC Authorized System Integrator (ASI) and A3 Certified Robot Integrator, Acieta delivers robotic palletizing solutions built to address your toughest manufacturing challenges and scale your operations.
10,000+
SYSTEMS INTEGRATED GLOBALLY
24/7
ON-CALL SERVICE TEAM
100 years
OF COMBINED EXPERTISE
320+
TEAM MEMBERS IN NORTH AMERICA
Streamline Operations with Robotic Palletizing Solutions
Acieta brings 100 years of combined expertise in industrial automation system integration and design. Acieta has integrated over 10,000 systems worldwide for manufacturers across a wide range of industries. Discover how we integrate fully automated pallet conveyor systems, bag palletizing robots, case palletizers, robotic case packers and other advanced palletizing robot solutions to optimize your operations.
If you don’t see exactly what you need, contact us—we’re confident we can help you achieve your automation goals.
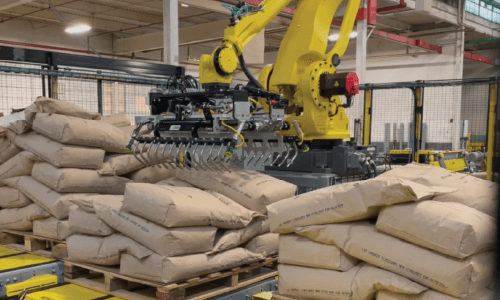
BAG PALLETIZING SYSTEMS:
- Compatible with bags made of:
-
- Woven polyproplene
- Paper
- Plastic
-
- Handles multiple bag sizes with a single EOAT
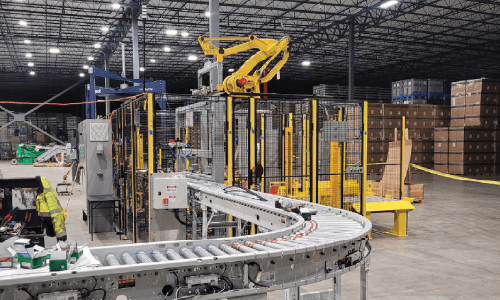
CASE CONVEYORS:
- Transports empty cases to the picking area and ensures precise results
- Carries filled cases to:
-
-
- Labeling
- Sealing
- Palletizing stages
-
-
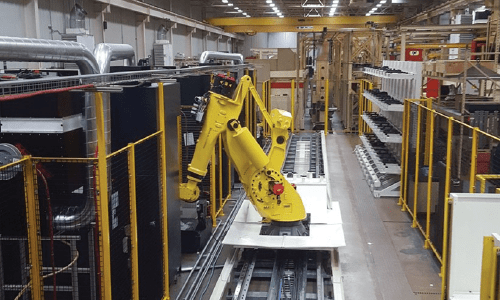
ROBOTIC TRANSPORT UNITS:
- Enables high-speed, precise movement of robotic arms across workstations
- Ideal for repetitive tasks
- Increases speed of production while reducing errors
- Improves the overall pick, pack and palletizing process
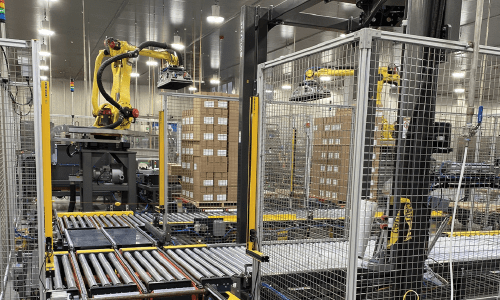
AUTOMATED PALLET CONVEYOR SYSTEMS:
- Facilitates safe and efficient movement of palletized loads
- Different types of pallet conveyors include:
-
-
-
- Roller conveyors
- Dual-load stackers
- Chain conveyors
- Gravity conveyors
- Pallet transfer conveyors
- 24V conveyors
-
-
-
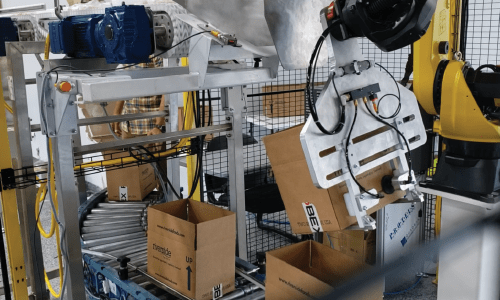
ROBOTIC CASE PACKER WITH VACUUM OR GRIPPER EOAT:
- Features a robotic case packer with:
-
-
- Vacuum EOAT
- Mechanical gripper
-
-
- Ensures efficient and precise product handling during packaging
- Accomodates various product shapes, sizes and weights
- Offers flexibility and reliability within operations
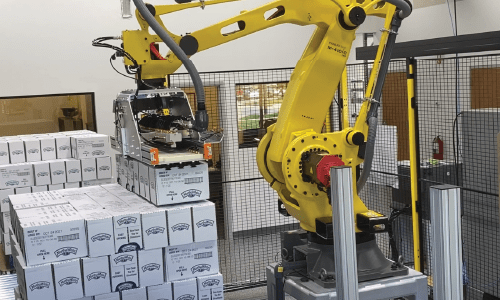
ROBOTIC CASE PALLETIZING WITH VACUUM, SPATULA OR CLAMP
- Vacuum EOAT applications:
-
-
- Ideal for lightweight or non-porous items
- Provides faster cycle times
- Handles complex palletizing patterns
-
-
- Spatula gripper applications are perfect for flat, rigid items like open-top cases
- Clamp grippers are best suited for simpler palletizing patterns
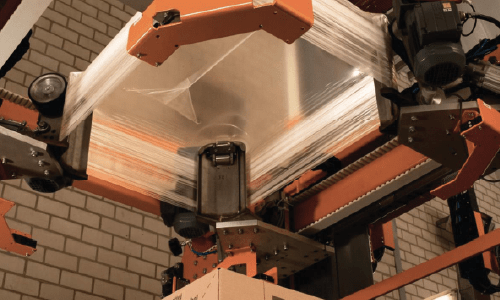
STRETCH HOODER
- Secures palletized loads with hood film for stability during transport and storage
- Automates product arrangement on pallets
- Positions hood film and measures load height
- Dispenses and forms bags based on load requirements
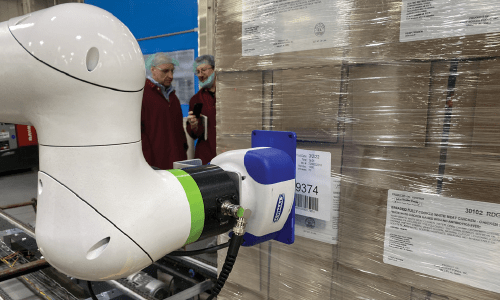
ROBOTIC LABELING:
- Integrates automated labeling in pick, pack, and palletizing systems
- Uses applicators or printers for accurate label application
- Robotic labeling incorporated when cost-effective
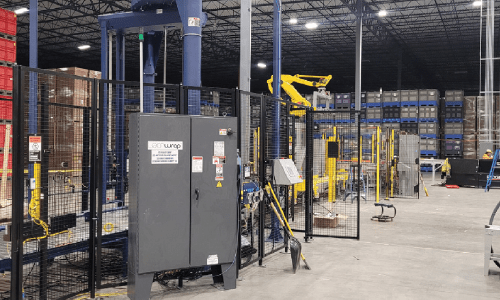
STRETCH WRAPPERS
- Automates packaging with precise control over wrapping tension, layers and patterns
- Ensures load stability and minimizes waste
- Integrates pick, pack and palletizing systems with stretch wrappers
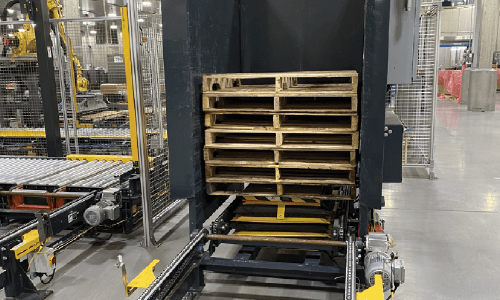
DUNNAGE SYSTEM
- Protects packages and prevents damage
- Provides tie surfaces
- Stabilizes loads
- Ensures product safety and avoids collisions during transport
Colbert Packaging
With over 150 different display cases and the need to manage four distinct pallet formats, Colbert Packaging, a leading manufacturer of corrugated packaging solutions faced significant challenges in their end-of-line packaging process. These complexities required a system capable of adapting to a wide variety of case configurations while maintaining a high throughput and minimizing manual intervention.
Together, we developed a custom robotic palletizing system was designed to address Colbert's specific operational challenges. This solution not only streamlined palletizing operations, but also incorporated end-to-end traceability, empowering Colbert Packaging to track performance in real-time and make data-driven decisions. This enhanced visibility ensures consistent quality, precision, and operational efficiency, while reducing human error.
Today, the system handles over 600 case types, providing the flexibility needed to meet the demands of an ever-evolving production environment.
Benefits of Robotic Palletizers
-
FLEXIBILITY & SCALABILITYDesigned with your future in mind, Acieta's custom palletizing solutions are tailor made to address your challenges now and grow with your business. These solutions are designed to easily adapt to changes in production requirements or product mix.
-
IMPROVED SUPPLY CHAIN RELIABILITYEnsure timely palletizing and depalletizing to meet demand fluctuations with robotic palletizing systems. Minimize inefficiencies, eliminate rework, and prevent delays in shipping and inventory management, keeping your operations efficient and responsive to changing needs.
-
ENHANCED DATA COLLECTIONPalletizing robots are integrated with sensors and software monitor product movement, delivering real-time data to optimize processes. This real-time tracking capability helps identify issues early, allowing your team to proactively address them and maintain smooth, efficient operations.
-
INCREASED PRODUCTIVITYAutomated palletizers handle the repetitive, monotonous tasks continuously without fatigue or distraction, ensuring faster, more consistent palletizing and depalletizing. Optimized cycle times maximize throughput leading to increased productivity.
-
FLOORPLAN OPTIMIZATIONRobots can operate efficiently in tight spaces, optimizing pallet patterns to enhance storage and transportation capacity. Many cobot palletizing solutions require little to no fencing, helping you make the most of your available floor space.
-
ENHANCED WORKPLACE SAFETYReduce work-related injury risks with automated pallet stackers. These systems manage heavy lifting effortlessly and enhance workplace safety while improving operational efficiency; positively enhancing the work environment for your staff and boosting profitability for your business.
-
EMPOWER EXISTING WORKFORCERobotic palletizing systems empower your team to handle more work without increasing headcount. By automating the repetitive palletizing tasks, your team can focus on higher-value, more strategic business initiatives.
-
DELIVER ROIRobotic palletizing solutions reduce rework and labor costs, driving ROI by enhancing process efficiency, quality and precision. These systems streamline operations, boost output, and deliver long-term value to keep your business competitive.
AMRs & AGVs Supporting End-of-Line Operations
Using autonomous mobile robots (AMRs) and autonomous guided vehicled (AGVs) in warehouse operations instead of human-operated forklifts, conveyor systems, or manual carts to move large volumes of material has proven to benefit numerous industries.
As a certified precision integrator for both MiR® and Seegrid, a FANUC Authorized System Integrator, and an A3 Certified Robot Integrator, we design custom robotic systems that bring industrial and collaborative robots together with AMRs and AGVs to bring you the most streamlined solution for your operations.
To learn more about utilizing AMRs or AGVs in your unique application:
Robotic Layered Case Packer
A global leader in responsible packaging approached Acieta to develop an automated palletizer for their complex production needs.
Their operation required a robotic case packer capable of safely and reliably handling over 300 different plastic bottle sizes. Additionally, the system needed to fill boxes in a soldier-packed format, accommodating both neck-up and neck-down orientations.
- Inconsistent packing quality
- Ergonomic strain on operators
- Safety concerns in the manual packaging process
- Frequent bag tearing, disrupting operations and reducing profitability
- Needed a reliable end-of-line packaging solution to ensure:
-
-
- Greater consistency
- Improved safety
- Reduced material waste
-
-
- Robotic case packer designed to handle 300+ bottle types
- Automated pallet stacker that auto generates stacking configuration based on user inputs
- Gentle handling features to prevent bag tearing
- Key components for safety and efficiency:
-
-
- Safety PLC, HMI, keyed entry gate switches, safety fencing, and vacuum conveyor with height adjustment
-
-
- Integrated with the molding machine for consistent, reliable operation
- Incoming molded bottle vacuum conveyor
- Leak test, pressure measurement
- FANUC M200iD, row picking robot, & vacuum EOAT
- FANUC M20iD/25, layer packing robot, & vacuum EOAT
- Blower-driven vacuum generation
- Pack position
- Incoming empty case conveyor
- Outgoing packed case conveyor
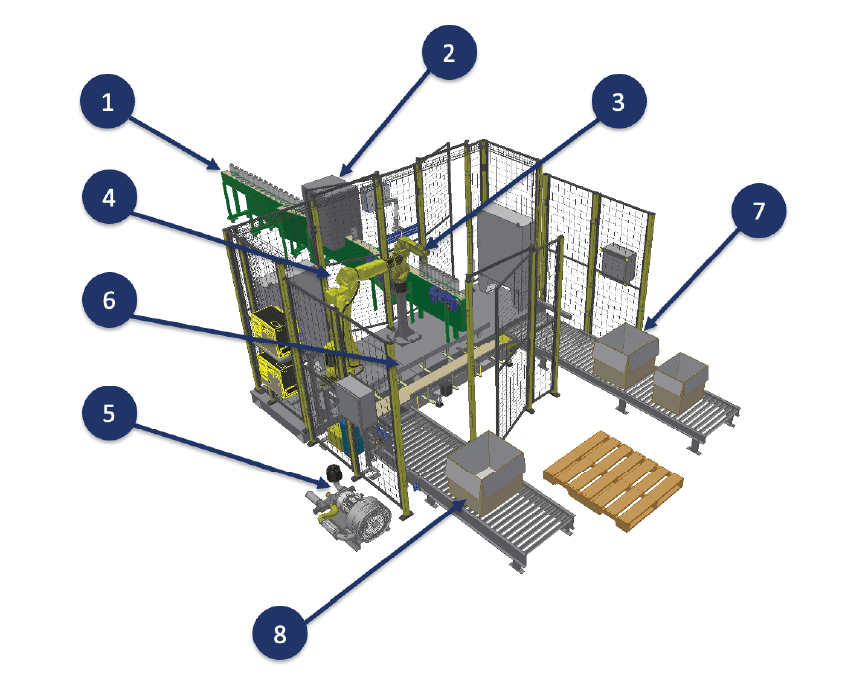
With Acieta, you truly become one team. From the very start of a project, the collaboration across departments creates a cohesive unit dedicated to success. The regular team meetings foster open communication, ensuring that everyone is aligned throughout the project lifecycle. This unity is vital for achieving project success.
Robotic Palletizer
Facing labor shortages and high turnover, a company struggling to meet production needs turned to Acieta for an automated palletizing solution. With issues in ergonomics and safety, they sought Acieta's expertise robotic system integrations and in designing a robotic palletizer to streamline operations and address these challenges.
- Needed sealed and open-topped cases with 300+ SKUs (14x6x6 to 24x22x28 in size)
- Reliant on manual labor to:
-
- Read barcodes
- Palletize cases
- Stretch wrap cases for complete end-of-line packaging
-
- Designed a robotic palletizing system that reads barcodes before palletizing
- Multi-functional EOAT with vacuum and spatula tooling
- Incorporated stretch wrapper before final pallet label application
- Enhanced safety features including banner photo eye sensors, fortress gate switches, and AXELENT safety fencing
- (6) Label apply device & barcode readers
- (6) 24V MDR case infeed conveyor with reject diverts
- (6) Pre-palletize barcode read for data trackings
- (2) Robot palletizer with multi-function EOAT tools
- (4) Layer & top-sheet stacks
- (3) Slider access doors
- (6) CDLR pallet build conveyors
- (1) Laser position t-car, traversing CDLR
- Manual tray forming/side load-in position
- Stretch wrapper (hidden for NDA)
- Final pallet label application
- (3) Pallet infeed label conveyor sets
- Robot pallet pick with custom EOAT and bottom sheet stack
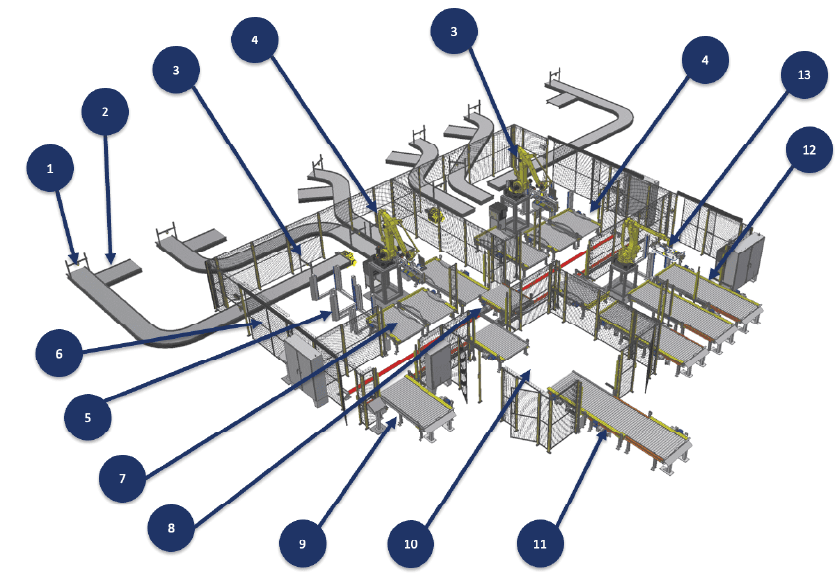